
Низкотемпературный каталитический термокрекинг гудрона в присутствии катализатора КМК-5
Без освоения новых деструктивных процессов переработки нефти, прежде всего — каталитического крекинга и гидрокрекинга вакуумных погонов, проблема углубления переработки нефти на данный момент не может быть решена. В свою очередь, освоение вышеназванных процессов сопровождается ростом числа установок висбрекинга гудрона или коксования. В последнее время многие НПЗ, имея в своем составе дорогостоящие комплексы по глубокой переработке, идут на «смягчение» температурного режима установок висбрекинга гудрона, снижая тем самым вероятность ускоренного закоксовывания змеевиков печи. Вместо регламентированной температуры нагрева гудрона, равной 460-465°С, на выходе из печи, как правило, поддерживается 445- 450°С. Это связано, прежде всего, с желанием уве- личить межремонтный пробег, перевести комплекс глубокой переработки нефти на 2-3-годичный цикл работы без остановок на текущий и капитальный ремонт и обеспечить достижение максимальной экономической эффективности производства.
Такое техническое решение имеет и явный недос- таток — вместо требуемой вязкости, не превыша- ющей 50 сСт при 100°С, крекинг-остаток на выходе с установки висбрекинга характеризуется вязкостью от 90 до 160 сСт. При этом возникает необходимость внепланового вовлечения средних дистиллятов (дизельные фракции и вакуумные погоны) на разбавление крекинг-остатка до требуемой вязкости. Получается нелепая ситуация — часть светлых дистиллятов тратится совершенно неквалифицированно вместо того, чтобы наращивать выход ценных светлых углеводородов. На эти цели заводы тратят до 25-30% дизельных фракций в расчёте на стабильный крекинг-остаток, чтобы привести качество последнего до норм ГОСТ-10585-13 по вязкости.
В настоящее время во всем мире суточная мощность установок висбрекинга и термокрекинга по переработке нефтяных остатков составляет 700 тыс.т. Более половины мощности этих процессов (55%) приходится на НПЗ Европы [1]. В России суммарная мощность процессов термокрекинга и висбрекинга тяжёлых нефтяных остатков (в основном гудрон) превышает 18 млн т в год. Другими словами, в настоящее время процесс висбрекинга гудрона для нефтеперерабатывающих предприятий является оп- ределяющим с точки зрения экономики и глубины переработки нефти, поскольку от его ритмичной работы зависит работа всего комплекса глубокой переработки нефти. Решение вопроса по выпуску стабильного крекинг-остатка с вязкостью менее 50 сСт без компаундирования с легкими дистиллятами яв- ляется сверх актуальным. По мнению авторов настоящей статьи, ответ на этот вопрос надо искать в улучшении работы самих установок висбрекинга.
Если рассматривать интенсификацию процесса висбрекинга тяжёлых нефтяных остатков, то, в принципе, имеется несколько модификаций этого процесса, которые могут положительно сказаться на работе установок висбрекинга с точки зрения снижения вязкости крекинг-остатка. Это такие процессы, как гидровисбрекинг, донорный висбрекинг и новый процесс, который недавно предложила компания ООО «КИНЭКС» совместно с Самарским государственным техническим университетом — «низкотемпературный каталитический термокрекинг» (патенты РФ 2626393, 2638834), в дальнейшем НТКТ. Конечной целью этих процессов является:
• достижение минимального значения вязкости крекинг-остатка;
• максимально возможный выход углеводородов, выкипающих до 360°С.
Рассмотрим основные условия протекания этих процессов.
Гидровисбрекинг — это термодеструктивный процесс переработки гудрона в среде водорода без внесения катализатора со стороны. Для такой технологии можно предположить, что металлоорганические соединения, содержащиеся в тяжёлых нефтяных остатках, могут выполнять роль катализатора гидрогенизационных реакций. Чтобы реализовать все преимущества данного процесса, необходимы достаточно высокие температуры (свыше 500°С) и давления (свыше 5,0 МПа). Соответствующая модификация обычной установки висбрекинга в таком направлении больше похожа не на реконструкцию, а на строительство самостоятельного, достаточно дорогого в материальном и техническом отношении процесса. Отметим, что при гидровисбрекинге гудрона для протекания реакций гидрогенолиза в любом случае необходима активация молекул водорода. Однако с ужесточением технологических параметров, вопреки ожиданиям, главным образом ускоряются реакции термического распада, а не реакции гидрогенолиза. По мнению авторов работ [2,3] при обозначенных выше технологических параметрах (Т = 500°С и Р = 5,0 МПа) водородосодержащий газ в большей степени выполняет роль турбулизатора реакционной массы.
Донорный висбрекинг — процесс крекинга, осуществляемый в отсутствии молекулярного водорода в зоне реакционной массы. Роль источника водорода в процессе выполняет специальный растворитель, обладающий способностью отдавать водород про- дуктам реакции, снижая тем самым отношение С:Н в продуктах термокрекинга. Донорный разбавитель должен хорошо смешиваться с сырьём, растворять асфальтены и легко генерировать атомарный водород. По существу, донорный термокрекинг аналогичен процессу гидровисбрекинга тяжёлых нефтяных остатков, только источником водорода выступает специальный органический растворитель. Расход све- жего донора, как правило, составляет 7-10% на кре- кируемое сырьё. Объёмная скорость подачи сырья как правило не превышает 1 ч-1, давление процесса поддерживается на уровне 2,5-5,5 МПа, температура достаточно высокая — 460-470°С, что, в свою очередь, приводит к повышенной коксуемости оборудования и трубопроводов. Проблема внедрения донорного висбрекинга нефтяных остатков состоит в поиске эффективного и недорогого донорного разбавителя.
На фоне рассмотренных процессов (гидровисбрекинг и донорный термокрекинг) весьма интересным представляется использование технологии низкотемпературного каталитического термокрекинга гудрона на базе типовой установки висбрекинга с применением катализатора «КМК-5», разработанного компанией ООО «КИНЭКС». При этом никаких реконструкций и капитальных вложений на модернизацию установки висбрекинга практически не требуется. Данный процесс интересен ещё и тем, что не требует использования никаких дополнительных источником водорода, существенно удорожающих и усложняющих технологию. Более того, процесс НТКТ практически не чувствителен к загрязняющим веществам, металлам, содержащимся в нефтяных остатках, и гетероатомным соединениям, поскольку свежий катализатор непрерывно поступает реактор.
Необходимо отметить, что в промышленных схемах подача катализатора в виде суспензии может осуществляться на участке трубопровода от печи до сокингкамеры. Данный технический приём полностью исключает коксование змеевика печи из-за отсутствия на этом участке катализатора и значительного снижения рабочих температур процесса (рис. 1).
Экспериментальные исследования висбрекинга гудрона по технологии НТКТ проводили на пилотной проточной установке с восходящим потоком реакционной массы в реакторе, установленной на кафедре «Химическая технология переработки нефти и газа» Самарского государственного технического университета. Принципиальная технологическая схема и описание работы установки приведены в [4].
Испытания проводили при давлении до 1,0 МПа и температурах от 400 до 455°С с гудронами, взятыми с двух заводов, которые принципиально отличаются друг от друга по физико-химическим свойствам (образцы «А» и «В»).
Первым в процессе НТКТ было изучено поведение образца А, полученного с одного из региональных НПЗ Центральной части России. Образец А использовался на НПЗ в качестве сырья установки

висбрекинга и представляет собой смесь следующе-го состава: гудрон — 75%, тяжёлый газойль к.к. — 12%, тяжёлый вакуумный погон — 12% и ловушечный продукт до 100% (табл. 1).
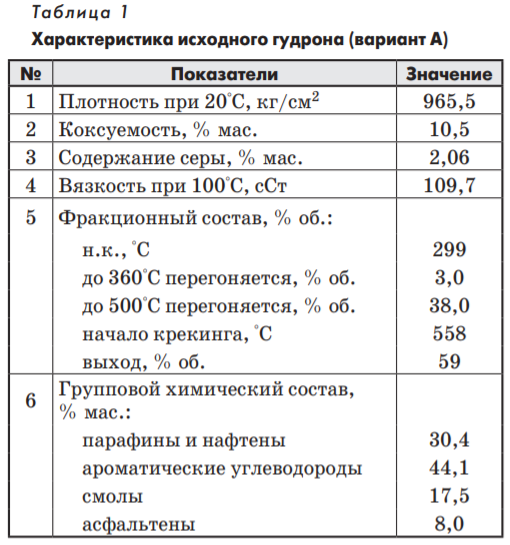
Переработка этого сырья (образец А) на действующей промышленной установке выполнялась в сле- дующих условиях:
• температура на выходе из печи 450-455°С;
• время нахождения реакционной массы в сокинг-камере — 30 мин.
При этом вязкость стабильного крекинг-остатка составляла 60-90 сСт при 100°С.
Фракция, выкипающая до 500°С в составе образ-ца А, представляет собой тяжёлый газойль каталитического крекинга (продукт с высоким содержанием полициклических ароматических соединений). Очевидно, что данная фракция не только мало активна в реакциях крекинга (все возможные реакции уже прошли в процессе каталитического крекинга), но и выступает коксогеном, осложняя процесс каталитического термокрекинга гудрона. По этой причине, по мнению авторов, на данном сырье весь потенциал низкотемпературного каталитического термокрекинга не был реализован, и глубина конверсии, о которой судили по величине вязкости крекинг-остатка после отгона бензиновой фракции н.к.-180°С, могла быть больше. Результаты экспериментов по процессу НТКТ образца А представлены в табл. 2.
Результаты, приведённые в табл. 2, говорят о высокой эффективности процесса НТКТ в присутствии катализатора КМК. Во всех проверенных режимах достигается значительное снижение вязкости крекинг-остатка по сравнению с работой блока висбрекинга гудрона промышленной установки. Важным является результат по снижению рабочей температуры процесса НТКТ на 20-25°С в сравнении с традиционным висбрекингом. Отметим, что стабильный крекинг-остаток во всех опытах имел вязкость не более 43,0 сСт при 100°С без разбавления дизельными фракциями, что полностью отвечает требованиям ГОСТ-10583-13 на мазуты топочные. Незначительное коксование наблюдалось в опыте при температуре 467°С. Выход кокса составил 1,3% мас. на пропущенный гудрон (определяли в составе крекинг-остатка).
Выход углеводородных газов во всех опытах находился в диапазоне 1,6-5,0% мас., а выход крекинг- остатка не падал ниже 95,0% мас. Особое внимание в данном эксперименте уделялось конверсии сырья
с получением светлых углеводородов, выкипающих до 360°С. В табл. 3 показаны результаты разгонки катализата, полученного в процессе НТКТ при температурах 420 и 430°С. Там же приведена вязкость остатка при 100°С, полученного после отгона фрак- ции н.к.-360°С. При этом надо отметить достаточно комфортные рабочие температуры процесса, в которых были получены данные результаты.
Характерные зависимости снижения вязкости
крекинг-остатка в присутствии 0,1% мас. катализатора КМК-5 от температуры и времени контакта представлены на рис. 2-4.
Каталитический эффект от введения КМК-5 в процесс термокрекинга гудрона характеризуется не только снижением температуры, при которой достигается требуемая по ГОСТ-10583-13 вязкость крекинг-остатка, но и образованием дополнительных количеств ценных светлых фракций, с одной стороны, и исключением их нецелевого использования на разбавление крекинг-остатка, с другой, увеличивая тем самым глубину переработки нефти.
На втором этапе был испытан образец гудрона Б с другого регионального НПЗ, который также явля- ется сырьём действующей установки висбрекинга. Показатели качества тестируемого продукта представлены в табл. 4-5.
Как видно из представленных данных, в составе образца гудрона Б отсутствуют фракции, выкипающие до 400°С, а доля фракций, выкипающих в диапазоне 400-500°С, не превышает 5% мас. Отличительная особенность второго образца — очень высокая вязкость и плотность, критически высокая величина коксуемости, равная 18,5% мас., значительное суммарное содержание металлов (выше 460 ppm) и высокое содержание серы. Сопоставляя значение коксуемости и содержание асфальтенов, можно предположить, что концентрация смол в представленном образце гудрона тоже достаточно высока.
Образец гудрона Б является достаточно сложным сырьем при переработке его по технологии висбрекинга с целью достижения вязкости крекинг-остатком не более 50 сСт из-за отсутствия вакуумных фракций и высокого показателя коксуемости.
Приступая к исследованию образца Б в условиях термического крекинга, в первую очередь на пилотной установке, были выполнены опыты по классическому висбрекингу гудрона без подачи катализатора КМК-5. Полученные результаты послужили базой для сравнения и оценки эффективности технологии НТКТ. Время пребывания нагретого гудрона в сокинг-камере (реакторе) составляло 10 мин. Результаты испытаний приведены в табл. 6.
Следует отметить, что результаты, полученные на пилотной установке, полностью согласуются с данными, которые были зафиксированы при соответствующих температурах во время работы промышленной установки висбрекинга для таких показателей, как вязкость крекинг-остатка, выход газа и крекинг-бензина. Это говорит о корректной работе пилотной установки с точки зрения воспроизводимости результатов процесса висбрекинга гудрона.
Необходимо отметить, что рабочий технологический режим промышленной установки висбрекинга гудрона на момент отбора пробы сырья (образец Б) выглядел следующим образом:
• температура перед сокинг-камерой — 443-445°С;
• время пребывания гудрона в сокинг-камере — 12 мин.
Вязкость стабильного крекинг-остатка в этих ус- ловиях составляла 85-107 сСт при 100°С.
Значения вязкости крекинг-остатка, полученные на промышленной установке, несколько выше требований, предъявляемых ГОСТ 10585-13 к ма- зуту топочному М-100. Поэтому для достижения требуемой вязкости крекинг-остатка на предприятии существует необходимость в его разбавлении дизельными фракциями. Попытки достичь требуемой вязкости крекинг-остатка повышением температуры выше 445°С, в первую очередь из-за высокой коксуемости сырья, сопровождаются возникнове- нием опасности закоксовывания змеевиков печи, трубопроводов и самой сокинг-камеры. Следствием этого может быть не только полная остановка блока висбрекинга гудрона, но и всего комплекса глубокой переработки нефти (в данном конкретном случае установки гидрокрекинга вакуумных погонов).
Исследование поведения образца гудрона Б в условиях процесса НТКТ проводили на той же пилотной установке и по той же технологии. Концентрация катализатора КМК-5 в опытах менялась в пределах 0,05-0,45% мас. в расчёте на крекируемый гудрон. Давление в реакторе варьировалось в диапазоне 0,8- 1,5 МПа в зависимости от температуры процесса. Давление в сокинг-камере промышленной установки висбрекинга при работе на аналогичном сырье составляло 1,6-1,7 МПа.
Первым шагом в исследовании каталитического термокрекинга образца Б также, как и образца А, было определение оптимальной концентрации катализатора КМК-5. На рис. 5 представлен график снижения вязкости крекинг-остатка от температуры процесса без катализатора (1 линия) и при дозировании 0,1% мас. КМК-5 в расчёте на сырьё (2 линия). Во всём изученном диапазоне температур вязкость крекинг-остатка, полученного по каталитической технологии, была ниже вязкости крекинг- остатка классического висбрекинга при одном и том же времени контакта, равном 10 мин.
Вторым по значимости показателем технологии НТКТ является время реакции. На рис. 6 дано графическое представление полученных результатов, из которых видно, что в случае классического висбрекинга гудрона при времени контакта 10 мин вязкость крекинг-остатка достигает нормы по ГОСТ 10585-13 при 460°С, а при использовании КМК-5 в количестве 0,1% мас. — при 445°С. При времени реакции, равном 30 мин, данный показатель вязкости достигается при температуре 435°С. Таким образом, применение технологии каталитического термокрекинга в присутствии 0,1% мас. КМК-5 и време- ни реакции 10 мин позволяет снизить температуру на выходе из печи на 15°С, а при времени реакции 30 мин — на 25°С.
Очевидно, что процесс НТКТ с использованием катализатора КМК-5 является более эффективным, как с точки зрения глубины снижения вязкости крекингостатка, температуры процесса и энергозатрат в целом. Применяемые рабочие температуры, время реакции и концентрация катализатора обес- печивают получение крекинг-остатка, отвечающего требованиям ГОСТ на мазуты топочные, и не сопровождаются углублением реакций уплотнения и коксования. Дополнительным положительным эф- фектом от применения разработанной технологии может быть увеличение межремонтного пробега установок висбрекинга.
Анализ данных, представленных в табл. 7, подтверждает вывод о глубокой конверсии сырья в условиях технологии каталитического термокрекинга. Так, при температуре 430°С и концентрации катализатора 0,1% мас. конверсия гудрона составила 26,5% мас. При температуре 440°С — 37,6% мас., а при 445°С — 47,8% мас. И это при том, что вязкость крекинг-остатка оставалась в норме, а температуры эксперимента не поднимались выше 445°С.
Надо отметить, что в составе светлых фракций (н.к.-360°С) доля дизельных дистиллятов (180- 360°С) преобладает. Аналогичная картина наблюдалась при переработке вакуумных газойлей по технологии НТКТ [4].
Отличительной особенностью каталитического термокрекинга является качество получаемых продуктов (табл. 8). Обращает на себя внимание тенденция по снижению серы в крекинг-остатке, а также низкое содержание непредельных углеводородов во всех узких крекинг-фракциях. Обычно крекинг- дистилляты традиционных термических процессов содержат в 5-8 раз больше непредельных соединений.
Такая ситуация, вероятно, свидетельствует о глубоком протекании реакций диспропорционирования в условиях процесса НТКТ на катализаторе КМК-5. Анализируя данные по качеству получаемых в процессе НТКТ легких дистиллятов, можно утверждать, что такие фракции вполне могут быть облагорожены на типовых установках гидроочистки, применяемых в производстве моторных топлив.
В предыдущей работе [4] в качестве растворителя для приготовления устойчивой суспензии катализатора КМК-5 было предложено использовать тяжёлый вакуумный погон, обладающий достаточно высокой вязкостью и плотностью, чтобы избежать седиментации частиц катализатора. Совместно с ПИ «Гипроникель» (СПб.) была проделана большая работа по поиску более простой и безопасной суспензионной системы для подачи катализатора в процесс НТКТ, что нашло отражение в данной публикации. Хорошие результаты показала смесь катализатора с химически очищенной водой в соотношении 50:50. Данная суспензия оказалось очень устойчивой. При подаче водной суспензии катализатора в процесс НТКТ в реакционной смеси появляется водяной пар, который кроме турбулизирующего эффекта способен ограничить глубину крекинга, сокращая степень образования кокса.
Первоначально вводимый в процесс НТКТ катализатор КМК-5 предполагалось оставлять в составе крекинг-остатка ввиду его ничтожно малого количества. В последнее время, с помощью специалистов ГУП «Институт нефтепереработки РБ» найдено простое техническое решение по удалению частиц отработанного катализатора и кокса из крекинг- остатка, что существенным образом повышает его качество.
Накопленный опыт по переработке тяжёлых остатков с использованием технологии НТКТ говорит о том, что эта технология может найти применение в подготовке высоковязких нефтей к транспорту, обеспечивая существенное снижение их вяз- кости.
В результате проведённых исследований можно сделать следующие выводы.
1. На пилотной проточной установке СамГТУ (кафедра «Химическая технология переработки нефти и газа») изучено влияние технологических парамет- ров процесса низкотемпературного каталитического термокрекинга гудрона на показатели качества и выход крекинг-остатка и получаемых светлых крекинг-дистиллятов.
2. Установлены оптимальные технологические параметры работы установок висбрекинга гудрона по технологии НТКТ при условии получения стабильного крекинг-остатка с вязкость менее 50 сСт при 100°С без дополнительного разбавления остатка дизельными фракциями.
3. Качество светлых крекинг-фракций вполне отвечает требованиям к сырью типовых установок гидроочистки моторных топлив.
4. Относительно широкий диапазон температур, принятый в качестве оптимального, объясняется варьированием свойств сырья (содержание асфальтенов, коксуемость, фракционный состав) в достаточно широком интервале. Для того, чтобы ниве- лировать избыточную реакционную активность катализатора при переработке сырья с высокой коксуемостью потребуются более низкие температуры, и наоборот, в случае сырья с пониженной коксуемостью температура каталитического процесса может быть более высокой.
5. Показано, что предлагаемый процесс НТКТ — эффективная технология переработки тяжёлых нефтяных остатков. Основывается на простых и недорогих технических решениях, которые позволяют без особых затрат на всех без исключения установках висбрекинга получать дополнительные объёмы светлых углеводородов и одновременно получать крекинг-остаток с показателями качества, отвечающими требованиям ГОСТ 10585-13 на мазут топочный марки М-100.
ЛИТЕРАТУРА
1. Нефтеперерабатывающая промышленность России и ведущих стран мира за 1995, 2003, 2004 гг. — М.: ОАО «ЦНИИТЭнефтехим», 2005. — 550 с. — (Аналит. обзор).
2. Хайрудинов И.Р., Тихонов А.А., Таушев В.В., Теля- шев Э.Г. Современное состояние и перспективы развития термических процессов переработки нефтяного сырья. — Уфа: Издательство ГУП ИНХП РБ, 2015. — 328 с.
3. Коптенармусов В.Б., Ипполитов Е.В., Клеонский И.Г. Использование водородсодержащего газа в качестве тур- булизатора при термическом крекинге мазута // Нефте- переработка и нефтехимия. — 1990. — № 12. — С. 10-12.
4. Коптенармусов В.Б., Катков А.Л., Малов Е.И., Пи- мерзин А.А., Цветков В.С. Низкотемпературный ката- литический термокрекинг вакуумных погонов в присут- ствии катализатора КМК-5 и водородсодержащего газа на проточной пилотной установке // Нефтепереработка и нефтехимия. — 2017. — № 3. — С. 7-15.